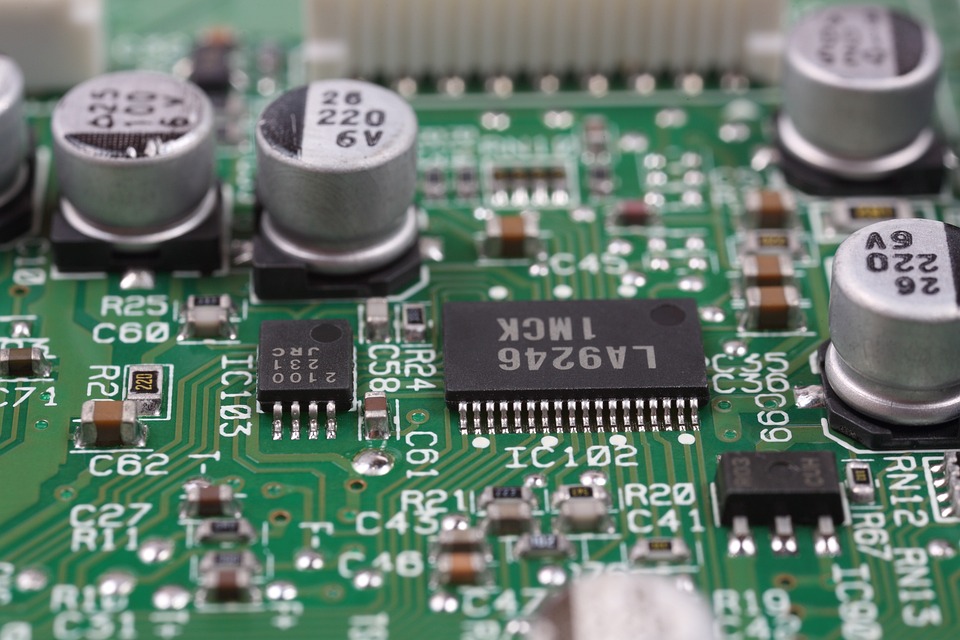
The Impact of PCB Design on PCB Manufacturing: Best Practices and Trade-Offs
The Impact of PCB Design on PCB Manufacturing: Best Practices and Trade-Offs
PCB design is a crucial step in the manufacturing process of printed circuit boards (PCBs). A well-designed PCB can ensure the successful production of high-quality boards, while a poorly designed PCB can lead to manufacturing issues, increased costs, and even product failure. In this article, we will explore the impact of PCB design on PCB manufacturing, highlighting best practices and trade-offs that designers should consider.
Design for Manufacturability (DFM)
Design for manufacturability (DFM) is a critical aspect of PCB design. DFM involves designing the PCB with manufacturability in mind, taking into account the capabilities and limitations of the manufacturing process. A DFM-aware design can reduce manufacturing costs, improve yield, and minimize defects.
Some key DFM considerations include:
- Component placement: Optimizing component placement can reduce manufacturing costs and improve PCB reliability. This includes minimizing the number of components, reducing component density, and avoiding sensitive components near edges.
- Routing: Effective routing can reduce manufacturing costs and improve PCB reliability. This includes minimizing the number of vias, reducing wire length, and avoiding complex routing.
- Layer stack-up: The layer stack-up of the PCB can significantly impact manufacturing costs and PCB reliability. This includes optimizing the number of layers, layer thickness, and layer materials.
- Component density: Component density can impact manufacturing costs and PCB reliability. This includes minimizing component density, reducing component size, and avoiding overcrowding.
Design for Test (DFT)
Design for test (DFT) is another critical aspect of PCB design. DFT involves designing the PCB with testability in mind, taking into account the capabilities and limitations of the testing process. A DFT-aware design can reduce testing costs, improve test efficiency, and minimize defects.
Some key DFT considerations include:
- Test access: Providing test access to all components and nodes can improve test efficiency and reduce testing costs. This includes adding test pads, reducing component density, and optimizing routing.
- Test point placement: Optimizing test point placement can improve test efficiency and reduce testing costs. This includes minimizing test point placement, reducing test point density, and avoiding sensitive components near edges.
- Scan design: Scan design can improve test efficiency and reduce testing costs. This includes optimizing scan chain length, reducing scan chain complexity, and avoiding sensitive components near edges.
Design for Assembly (DFA)
Design for assembly (DFA) is another critical aspect of PCB design. DFA involves designing the PCB with assembly in mind, taking into account the capabilities and limitations of the assembly process. A DFA-aware design can reduce assembly costs, improve assembly efficiency, and minimize defects.
Some key DFA considerations include:
- Component placement: Optimizing component placement can reduce assembly costs and improve PCB reliability. This includes minimizing the number of components, reducing component density, and avoiding sensitive components near edges.
- Component orientation: Optimizing component orientation can reduce assembly costs and improve PCB reliability. This includes minimizing component orientation, reducing component size, and avoiding overcrowding.
- Pad shape and size: Optimizing pad shape and size can reduce assembly costs and improve PCB reliability. This includes minimizing pad size, reducing pad density, and avoiding sensitive components near edges.
Design for Reliability (DFR)
Design for reliability (DFR) is another critical aspect of PCB design. DFR involves designing the PCB with reliability in mind, taking into account the capabilities and limitations of the PCB and its components. A DFR-aware design can improve PCB reliability, reduce failure rates, and minimize maintenance costs.
Some key DFR considerations include:
- Component selection: Selecting high-reliability components can improve PCB reliability and reduce failure rates. This includes selecting components with high MTBF, minimizing component density, and avoiding sensitive components near edges.
- PCB material selection: Selecting high-reliability PCB materials can improve PCB reliability and reduce failure rates. This includes selecting materials with high thermal conductivity, minimizing PCB thickness, and avoiding sensitive components near edges.
- Thermal management: Effective thermal management can improve PCB reliability and reduce failure rates. This includes optimizing thermal design, minimizing thermal gradients, and avoiding sensitive components near edges.
Trade-Offs
PCB design is often a trade-off between competing design goals. For example:
- Cost vs. performance: PCB design may require trade-offs between cost and performance. For example, using high-reliability components may increase costs, but improve PCB reliability.
- Manufacturability vs. design complexity: PCB design may require trade-offs between manufacturability and design complexity. For example, a simple design may be easier to manufacture, but may not meet performance requirements.
- Reliability vs. cost: PCB design may require trade-offs between reliability and cost. For example, using high-reliability components may increase costs, but improve PCB reliability.
Conclusion
In conclusion, PCB design has a significant impact on PCB manufacturing. By considering DFM, DFT, DFA, and DFR, designers can optimize PCB design for manufacturability, testability, assembly, and reliability. By understanding the trade-offs between competing design goals, designers can make informed decisions that balance cost, performance, and reliability. By following best practices and considering trade-offs, designers can create high-quality PCBs that meet performance requirements and minimize manufacturing costs.
FAQs
Q: What is Design for Manufacturability (DFM)?
A: DFM is the process of designing a PCB with manufacturability in mind, taking into account the capabilities and limitations of the manufacturing process.
Q: What is Design for Test (DFT)?
A: DFT is the process of designing a PCB with testability in mind, taking into account the capabilities and limitations of the testing process.
Q: What is Design for Assembly (DFA)?
A: DFA is the process of designing a PCB with assembly in mind, taking into account the capabilities and limitations of the assembly process.
Q: What is Design for Reliability (DFR)?
A: DFR is the process of designing a PCB with reliability in mind, taking into account the capabilities and limitations of the PCB and its components.
Q: What are some common trade-offs in PCB design?
A: Some common trade-offs in PCB design include cost vs. performance, manufacturability vs. design complexity, and reliability vs. cost.
Q: How can I optimize my PCB design for manufacturability, testability, assembly, and reliability?
A: You can optimize your PCB design by considering DFM, DFT, DFA, and DFR, and by understanding the trade-offs between competing design goals. By following best practices and considering trade-offs, you can create high-quality PCBs that meet performance requirements and minimize manufacturing costs.