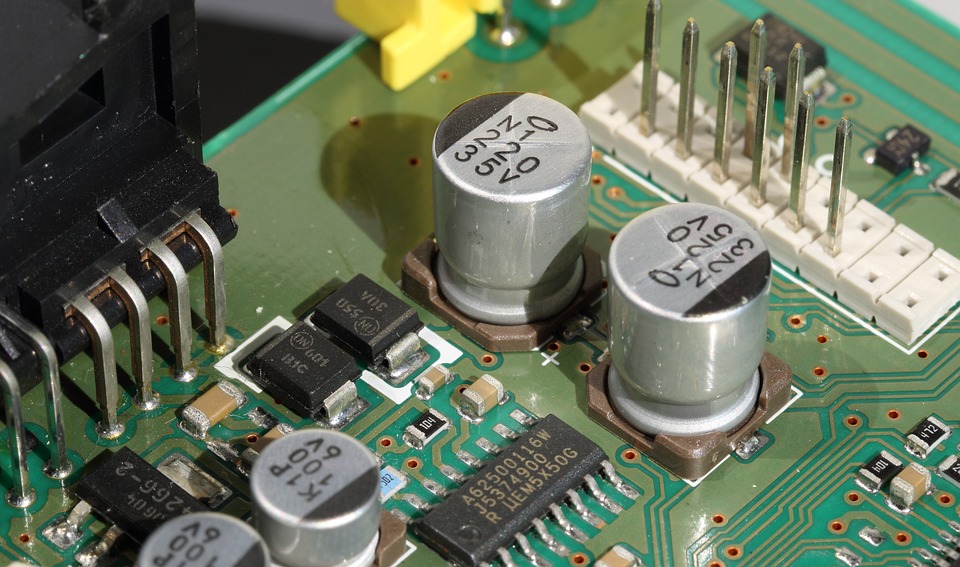
The Benefits of PCB Design for Manufacturability (DFM): A Guide to Efficient Design
PCB design for manufacturability (DFM) is a critical aspect of the printed circuit board (PCB) design process. It involves designing the PCB with manufacturability in mind, taking into account the production process, materials, and equipment used to manufacture the board. The benefits of DFM are numerous, and in this article, we will explore the advantages of incorporating DFM into your PCB design process.
Improved Design Efficiency
One of the primary benefits of DFM is improved design efficiency. By considering manufacturability during the design process, designers can avoid costly rework and redesigns, which can significantly reduce the time and resources required to complete a project. With DFM, designers can focus on creating a design that meets the required specifications and is optimized for production.
DFM also enables designers to identify and address potential design flaws and errors early in the design process, reducing the risk of costly redesigns and rework. This approach also enables designers to make informed decisions about the design, taking into account the production process and materials used.
Reduced Manufacturing Costs
Another significant benefit of DFM is reduced manufacturing costs. By designing the PCB with manufacturability in mind, designers can reduce the cost of production by minimizing the use of complex and expensive manufacturing processes. This can include reducing the number of layers, minimizing the use of specialized materials, and optimizing the design for efficient production.
DFM can also help reduce waste and scrap rates, which can be significant in PCB manufacturing. By designing the PCB with manufacturability in mind, designers can minimize the risk of defects and errors, reducing the amount of waste and scrap generated during production.
Improved Quality and Reliability
DFM can also improve the quality and reliability of the final product. By designing the PCB with manufacturability in mind, designers can ensure that the board is optimized for production, reducing the risk of defects and errors. This can include designing the board with redundant components, minimizing the use of complex and sensitive components, and optimizing the design for efficient production.
DFM can also help improve the reliability of the final product by reducing the risk of mechanical stress and vibration. By designing the PCB with manufacturability in mind, designers can minimize the risk of mechanical stress and vibration, reducing the risk of component failure and improving the overall reliability of the final product.
Enhanced Collaboration and Communication
DFM can also enhance collaboration and communication between designers, manufacturers, and other stakeholders. By considering manufacturability during the design process, designers can ensure that the design meets the requirements of the production process and materials used. This can include collaborating with manufacturers to ensure that the design is optimized for production, and communicating with other stakeholders to ensure that the design meets their requirements.
DFM can also help improve communication between designers and manufacturers by providing a common language and set of standards for the design process. This can include using standardized design files and formats, and collaborating with manufacturers to develop and implement design standards and guidelines.
Conclusion
In conclusion, PCB design for manufacturability (DFM) is a critical aspect of the PCB design process. By considering manufacturability during the design process, designers can improve design efficiency, reduce manufacturing costs, improve quality and reliability, and enhance collaboration and communication. DFM is an essential step in the PCB design process, and by incorporating it into your design process, you can ensure that your designs are optimized for production and meet the required specifications.
FAQs
Q: What is PCB design for manufacturability (DFM)?
A: PCB design for manufacturability (DFM) is the process of designing printed circuit boards (PCBs) with manufacturability in mind, taking into account the production process, materials, and equipment used to manufacture the board.
Q: Why is DFM important?
A: DFM is important because it enables designers to create designs that are optimized for production, reducing the risk of costly redesigns and rework, and improving the quality and reliability of the final product.
Q: How can I incorporate DFM into my design process?
A: You can incorporate DFM into your design process by considering manufacturability during the design process, collaborating with manufacturers, and using standardized design files and formats.
Q: What are the benefits of DFM?
A: The benefits of DFM include improved design efficiency, reduced manufacturing costs, improved quality and reliability, and enhanced collaboration and communication.
Q: Can DFM be used for all types of PCBs?
A: Yes, DFM can be used for all types of PCBs, from simple to complex designs. However, the extent to which DFM is used may vary depending on the complexity and requirements of the design.
Q: Is DFM a one-time process?
A: No, DFM is an ongoing process that should be integrated into the design process from the beginning to the end of the project. It is an iterative process that requires continuous collaboration and communication between designers, manufacturers, and other stakeholders.