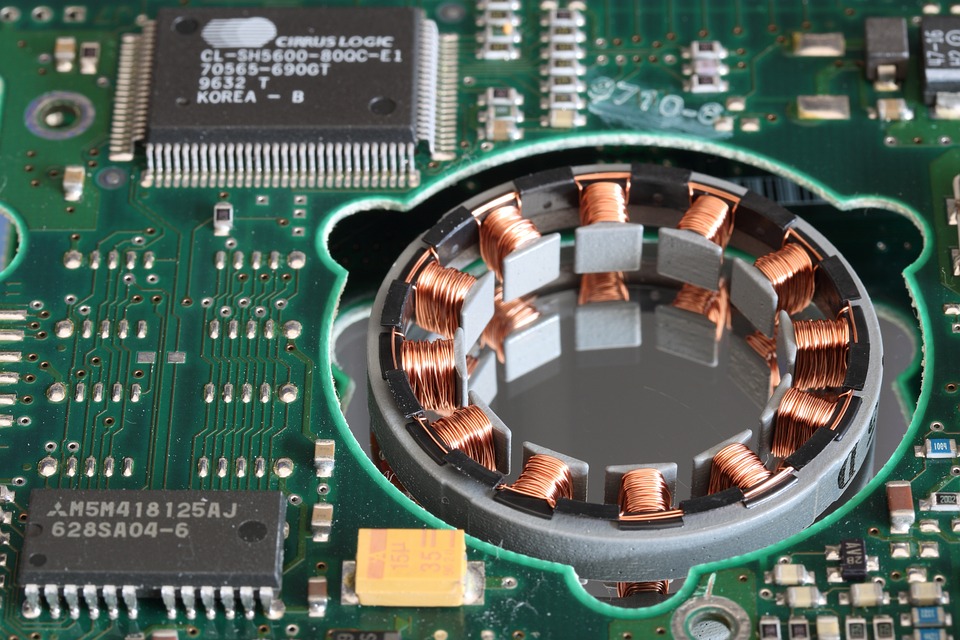
The Advantages of Surface Mount Technology (SMT) in PCB Assembly
The Advantages of Surface Mount Technology (SMT) in PCB Assembly
In the world of printed circuit board (PCB) assembly, Surface Mount Technology (SMT) has revolutionized the way components are attached to a board. Since its introduction in the 1960s, SMT has become the preferred method for assembling a wide range of electronic components, from simple printed circuit boards to complex systems-on-chip (SoCs). In this article, we’ll explore the advantages of SMT in PCB assembly and why it’s the most popular method for assembling electronic devices.
Advantages of SMT in PCB Assembly
1. Increased Efficiency: SMT allows for faster assembly times and reduces labor costs. With SMT, components are placed on the board in a more efficient manner, reducing the need for wire bonding and through-hole technology. This results in a significant reduction in assembly time and costs.
2. Compact Design: SMT enables the use of smaller components, which leads to compact designs, reduced size, and increased portability. This is particularly important in applications where space is limited, such as mobile devices, Internet of Things (IoT) devices, and wearable technology.
3. Improved Reliability: SMT components are less prone to damage and have a longer lifespan compared to traditional through-hole components. This is because SMT components are designed to withstand environmental factors such as temperature fluctuations, humidity, and vibrations.
4. : SMT components are designed to be easily removable and replaceable, making it simpler to repair or upgrade devices. This is particularly important in critical applications where downtime is costly or unacceptable.
5. Cost Savings: SMT components are often less expensive than traditional through-hole components, reducing the overall cost of PCB assembly.
6. Increased Flexibility: SMT components can be placed on both sides of the board, increasing the potential for complex circuit designs and increased functionality.
7. Reduced Design Complexity: SMT enables the use of surface-mount design rules, which simplify the design process and reduce the risk of errors.
8. Improved Thermal Management: SMT components are designed to dissipate heat effectively, which is critical in high-power applications where thermal management is essential.
9. Enhanced Component Performance: SMT components are designed to optimize performance, allowing for improved signal integrity, reduced signal loss, and increased reliability.
Conclusion
In conclusion, Surface Mount Technology (SMT) has revolutionized the way electronic devices are assembled, offering numerous advantages over traditional through-hole technology. The benefits of SMT include increased efficiency, compact design, improved reliability, ease of component replacement, cost savings, increased flexibility, reduced design complexity, improved thermal management, and enhanced component performance. As the demand for electronic devices continues to grow, SMT is expected to play a crucial role in the development of tomorrow’s technology.
FAQs
Q: What is Surface Mount Technology (SMT)?
A: SMT is a method of attaching electronic components to a printed circuit board (PCB) by placing them on the surface of the board.
Q: What are the advantages of SMT over through-hole technology?
A: SMT offers increased efficiency, compact design, improved reliability, ease of component replacement, cost savings, increased flexibility, reduced design complexity, improved thermal management, and enhanced component performance.
Q: What are the limitations of SMT?
A: SMT has limitations when it comes to complex or high-frequency applications, where traditional through-hole technology may be more suitable. Additionally, SMT can be more challenging for inexperienced assemblers due to the need for precise placement and orientation of components.
Q: How do I choose the right SMT components for my project?
A: When selecting SMT components, consider factors such as the component’s reliability, availability, and price. It’s also important to ensure compatibility with the PCB design and the intended application.