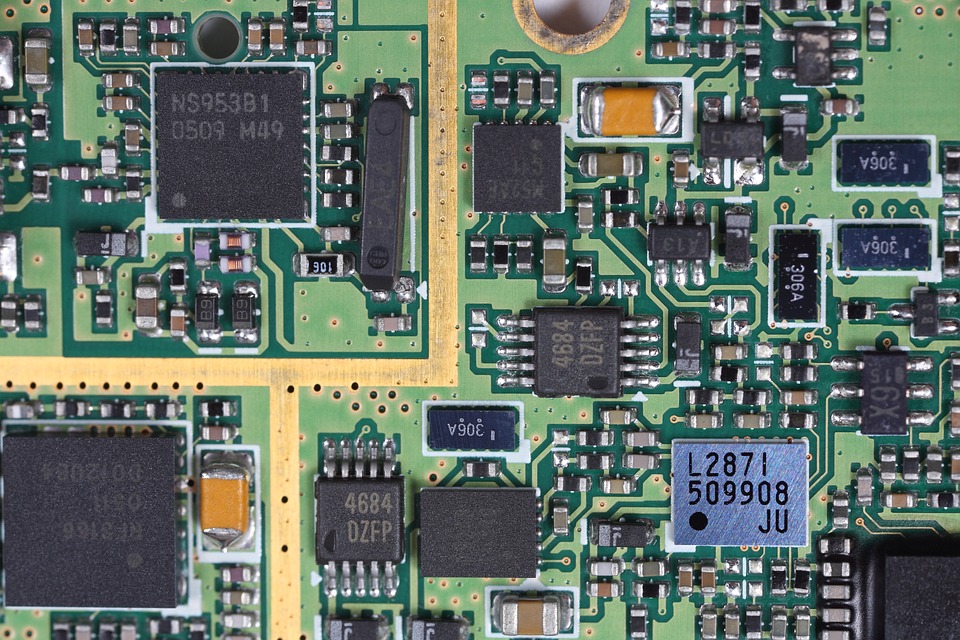
PCB Failure Analysis: What to Do When Your Board Fails
PCB Failure Analysis: What to Do When Your Board Fails
Introduction
PCBs (Printed Circuit Boards) are the backbone of modern electronic devices, providing a platform for the assembly and connection of electronic components. With the increasing complexity of electronic designs, PCB failures can be frustrating and costly to diagnose and resolve. When a PCB fails, it’s essential to conduct a thorough failure analysis to identify the root cause and implement corrective measures to prevent similar failures in the future.
Failure Analysis Techniques
PCB failure analysis involves the application of various techniques to diagnose and identify the root cause of the failure. Some common techniques used in PCB failure analysis include:
* Visual inspection: This involves a detailed visual examination of the PCB to identify any visible signs of damage or wear.
* Electrical testing: This includes testing the PCB’s electrical integrity using instruments such as oscilloscopes and multimeters.
* Chemical testing: This involves testing the PCB’s chemical composition to identify any contamination or damage.
* Imaging techniques: Techniques such as X-ray, ultrasonic, and thermal imaging are used to visualize internal structures and detect defects.
Common Causes of PCB Failure
PCB failures can occur due to various factors, including:
* Design flaws: Inadequate design considerations, such as inadequate component placement or routing, can lead to PCB failures.
* Manufacturing defects: Defects such as misprinted or damaged layers, contamination, or improper assembly can cause PCB failures.
* Environmental factors: Exposure to harsh environmental conditions such as temperature, humidity, or vibration can cause PCB failures.
* Component failures: Failures of individual components, such as capacitors, resistors, or integrated circuits, can also cause PCB failures.
Steps for Conducting PCB Failure Analysis
Conducting a thorough PCB failure analysis requires a systematic approach. The following steps can help guide the analysis:
1. Gather information: Collect information about the failed PCB, including the design specifications, manufacturing process, and operating conditions.
2. Visual inspection: Perform a visual inspection of the PCB to identify any visible signs of damage or wear.
3. Electrical testing: Conduct electrical testing to determine the extent of the failure and identify any symptoms.
4. Component testing: Test individual components to determine their functionality and identify any failures.
5. Analyze data: Analyze the data collected during the testing and inspection to identify the root cause of the failure.
6. Implement corrective measures: Implement corrective measures to prevent similar failures in the future, such as re-designing the PCB or changing the manufacturing process.
Best Practices for PCB Design and Manufacturing
To prevent PCB failures, it’s essential to follow best practices for PCB design and manufacturing. Some best practices include:
* Use of industry-standard design rules and guidelines.
* Implementation of design-for-testability (DFT) techniques.
* Use of reliable components and suppliers.
* Implementation of quality control measures during manufacturing.
* Testing and validation of PCBs before they are released to production.
Conclusion
PCB failure analysis is a critical step in the diagnosis and resolution of PCB failures. By understanding the common causes of PCB failures, using a systematic approach to analysis, and implementing best practices for PCB design and manufacturing, manufacturers can reduce the likelihood of PCB failures and minimize the impact of failures when they do occur.