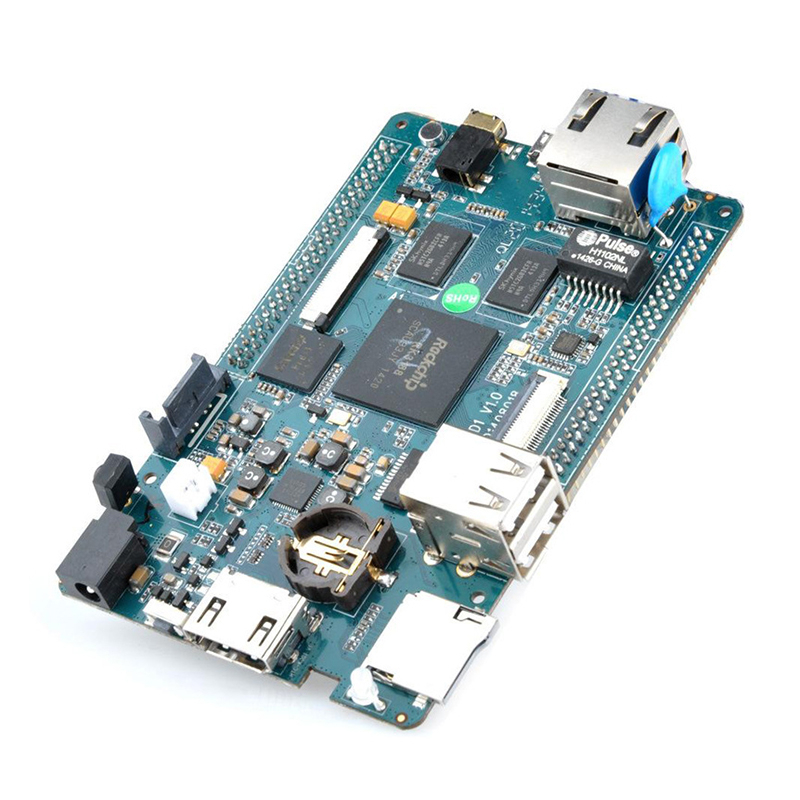
How to assembe own pcb solder mask
Mastering the Art of PCB prototypes are vital for testing designs before full production. Solder Mask: Your Ultimate Guide to Perfecting Circuit Boards at Home
This article delves into the intricate world of printed circuit boards (PCBs), focusing on the essential role of the solder paste is often used for better adhesion. mask using advanced techniques is essential for quality.. We’ll explore how to make your own PCB and understand why the solder mask is crucial for achieving professional-quality results. Whether you’re a hobbyist or a professional, this guide will equip you with the knowledge and techniques to enhance your PCB projects that involve creating a PCB prototype. If you are a PCB design company or electrical manufacturing business, this information is particularly valuable. We, as a leading PCB and PCB assembly manufacturing plant, aim to empower you with insights that can transform your approach to PCB design and manufacturing.
Table of Contents
Article Outline
- What is a PCB and Why is it Important?
- What Exactly is Solder Mask and Why Do You Need It on Your PCB?
- Different Types of Solder: Which One is Right for Your PCB?
- How to Choose the Right Solder Mask Material?
- Can You Make a PCB at Home?
- Step-by-Step Guide to Applying Solder Mask to Your PCB
- What are the Common Mistakes in Solder Mask Application and How to Avoid Them?
- How Does UV Light Play a Role in PCB Solder Masking?
- How to Inspect Your PCB After Solder Mask Application?
- Advanced Techniques in PCB Design: Mastering Solder Mask Layer
What is a PCB and Why is it Important?
A printed circuit board (PCB) is the foundational element of most electronic devices. It mechanically supports and electrically connects electronic components using conductive pathways, tracks, or signal traces etched from copper sheets laminated onto a non-conductive substrate. I’ve seen firsthand in our PCB manufacturing plant how crucial a well-designed PCB is to the functionality and reliability of any electronic product.
PCBs can be single-sided (one copper layer), double-sided (two copper layers on both sides of one substrate layer), or multi-layer (outer and inner layers of copper, alternating with layers of substrate). As a PCB and PCB assembly provider, we understand that PCBs are not just components; they are the heart of modern electronics. They are integral in devices ranging from simple gadgets like digital clocks to complex systems like computers and smartphones. Without PCBs, modern electronic devices would be significantly larger, less efficient, and more expensive to produce. The evolution of PCB technology has enabled the miniaturization and increased functionality of electronic devices.
What Exactly is Solder Mask and Why Do You Need It on Your PCB?
Solder mask, also known as solder resist, is a thin, lacquer-like layer of polymer applied to the copper traces of a PCB. Its primary function is to prevent solder from bridging between closely spaced solder pads, which can cause short circuits due to oxidation. If you aim to make a PCB or engage in any PCB project, understanding the role of solder mask is essential.
In our experience, the application of solder mask is a critical step in PCB fabrication. A solder mask is not always used for hand-soldered assemblies but is essential for mass-produced PCBs that are soldered automatically using reflow or wave soldering techniques. It is typically green but is also available in many other colors. The solder mask also protects the PCB from environmental factors like dust and moisture, extending the lifespan of the circuit board. As experts in PCB manufacturing, we often emphasize to our clients, especially PCB design companies, the importance of a well-applied solder mask in ensuring product quality and durability.
Different Types of Solder: Which One is Right for Your PCB?
Solder is a metal alloy used to create a strong permanent bond between metal workpieces. In PCB assembly, solder forms the electrical connections between the components and the PCB. There are various types of solder, each with unique properties. The most common solder composition used to be a 60/40 tin/lead mix, but due to health concerns, lead-free alternatives are now more prevalent.
Here’s a table summarizing common solder types:
Solder Type | Composition | Melting Point (°C) | Use Case |
---|---|---|---|
Tin-Lead | 60% Tin, 40% Lead | 183-190 | General, now less common |
Lead-Free | 99.3% Tin, 0.7% Copper | 217-220 | Environmentally friendly, now standard |
Silver Alloy | Tin, Copper, Silver | 217-220 | High conductivity, high-end audio |
Bismuth-Tin Solder | Tin, Bismuth | 138-200 | Low temperature soldering, sensitive components |
Choosing the right type of solder depends on the specific requirements of your PCB and the components you are using. For instance, lead-free solder is ideal for applications where environmental regulations are stringent. In our PCB manufacturing processes, we carefully select the solder type based on the client’s needs, ensuring optimal performance and compliance.
How to Choose the Right Solder Mask Material?
The solder mask material selection is a critical decision in PCB design. The most common solder mask materials are epoxy liquid that is thermoset, liquid photoimageable solder mask (LPSM) inks, and dry film photoimageable solder mask (DFSM). UV curable solder mask has gained popularity due to its quick curing time under solder mask using light. UV light.
Choosing the right mask material depends on factors such as the complexity of the PCB, the required resolution, and the operating environment of the final product. For instance, LPSM is excellent for high-density PCB designs, while DFSM is better suited for simpler designs or prototypes. From my experience in the field, understanding the properties of each solder mask material helps in making an informed decision that can significantly impact the PCB’s performance.
Can You Make a PCB at Home?
Yes, you can make a PCB at home. This can be a rewarding project for hobbyists and professionals alike. The process typically involves designing the PCB layout using CAD software, printing it onto a transparency film, transferring the design to a copper-clad board, etching away the unwanted copper, drilling holes for components, and finally, applying the solder mask.
While making a PCB at home offers flexibility and a great learning experience, it requires precision and patience. For more complex designs or higher volumes, it’s often more practical to rely on professional PCB manufacturing services, like those we provide. Our expertise and advanced equipment ensure high-quality results, especially for intricate PCB designs.
Step-by-Step Guide to Applying Solder Mask to Your PCB
Applying solder mask to your PCB is a critical step in ensuring the longevity and functionality of your circuit board. Here’s a simple step-by-step guide:
- Preparation: Ensure your PCB is clean and free of any dust or oil. This can be achieved by using isopropyl alcohol to gently wipe the surface. It’s crucial to handle the PCB by the edges to avoid leaving fingerprints on the copper traces.
- Applying the Solder Mask: If using a liquid photoimageable solder mask (LPSM), apply it evenly across the PCB surface. You can use a squeegee or a similar tool for uniform distribution. For dry film solder masks, carefully laminate the film onto the PCB, ensuring there are no air bubbles.
- Exposure: Place a transparency film with your solder mask pattern over the PCB. Expose the PCB to UV light. The exposure time will depend on the type of solder mask and the UV light source.
- Developing: After exposure, develop the PCB in a developing solution. This will remove the unexposed solder mask, revealing the copper pads where components will be soldered to assemble a PCB.
- Curing: Finally, we will place the PCB in the milling machine. cure the solder mask under UV light or in an oven, depending on the solder mask type. This step hardens the solder mask, making it durable.
Here are some additional tips from my experience:
- Always work in a well-ventilated area, especially when using chemicals.
- Wear gloves and safety glasses to protect yourself from chemicals.
- Follow the manufacturer’s instructions for the specific solder mask product you are using.
- Test your process on a scrap PCB prototype before finalizing. PCB before applying it to your final project.
Remember, the key to a successful solder mask application is patience and precision. If you’re unsure about any step, don’t hesitate to reach out to us. Our team has extensive experience in PCB manufacturing and can offer guidance to ensure your project is a success.
What are the Common Mistakes in Solder Mask Application and How to Avoid Them?
Common mistakes in solder mask application include uneven coating, misalignment of the solder mask layer, and incomplete curing. Uneven coating can lead to some areas being unprotected, while misalignment can expose areas that should be covered, leading to potential solder bridges.
In our PCB manufacturing plant, we use automated processes to minimize these errors. For DIY projects, it’s crucial to double-check the alignment and ensure even solder mask distribution. Proper curing is also essential – using the correct UV light intensity and duration is key to achieving a durable solder mask.
How Does UV Light Play a Role in PCB Solder Masking?
UV light plays a crucial role in the curing process of photoimageable solder mask using advanced techniques. solder masks. When the solder mask is exposed to UV light, it undergoes a chemical reaction that hardens the exposed areas. This process is essential for creating a durable and precise solder mask layer.
The exposure time and intensity of the UV light are critical parameters that need to be controlled precisely. In our facility, we use calibrated tools desktop pcb milling machine for precision. UV light sources to ensure consistent and reliable curing. For those working on PCB projects at home, understanding the specific requirements of your UV curable solder mask is vital for success.
How to Inspect Your PCB After Solder Mask Application?
Inspecting your PCB after solder mask application is a crucial step to ensure quality. Here’s what you should look for:
- Alignment: Check if the solder mask accurately covers the intended areas and leaves the solder pads exposed. Misalignment can lead to soldering issues later on.
- Uniformity: The solder mask should have an even thickness across the PCB. Uneven coating can result in weak spots that may fail under stress or during the soldering process.
- Adhesion: Gently test the solder mask’s adhesion to the PCB surface. It should be firmly attached without any peeling or bubbling.
- Curing: Ensure the solder mask is fully cured. It should be hard and not tacky to the touch. Incomplete curing can compromise its protective properties.
If you find any issues during the inspection, it’s better to address them before proceeding to the next steps of PCB assembly. From my experience, a thorough inspection can save a lot of time and resources in the long run. If you’re working on a complex PCB design, feel free to reach out to us for a professional inspection. Our advanced equipment and expertise can help identify and resolve any potential issues.
Advanced Techniques in PCB Design: Mastering Solder Mask Layer
In advanced PCB design, the precise bantam tools desktop pcb milling machine is essential. solder mask layer plays a critical role beyond just preventing solder bridges. It can be used to create dams to control solder flow during reflow, define specific areas for selective plating, or even as an additional dielectric layer in high-frequency applications.
Mastering the solder mask layer involves understanding how it interacts with other layers of the PCB, such as the copper and silkscreen layers. It requires precise control over the solder mask opening around pads and vias to ensure proper solder joints. Advanced CAD tools allow for detailed design and simulation of the solder mask layer, helping to optimize the PCB for manufacturing and performance. In our PCB manufacturing processes, we leverage these advanced techniques to deliver high-quality PCBs that meet the demanding requirements of modern electronics.

FAQs
What is the purpose of a solder mask on a PCB?
The primary purpose of a solder mask is to prevent solder bridges from forming between closely spaced solder pads, which can cause short circuits. It also protects the PCB from environmental factors like dust and moisture.
Can I use any type of solder mask for my PCB project?
The choice of solder mask depends on various factors, including the complexity of your PCB design, the operating environment, and your manufacturing process. Common types include liquid photoimageable solder mask (LPSM) and dry film solder mask (DFSM).
How do I know if my solder mask is properly cured?
A properly cured solder mask will be hard and not tacky to the touch. It should also adhere firmly to the PCB surface without any peeling or bubbling.
Is it necessary to use UV light for curing solder masks?
UV light is essential for curing photoimageable solder masks. The exposure time and intensity depend on the specific solder mask material and should be followed according to the manufacturer’s instructions.
How long does it take to cure a UV curable solder mask?
The curing time for a UV curable solder mask varies depending on the specific product and the intensity of the UV light source. Typically, it ranges from a few seconds to several minutes. Always refer to the manufacturer’s datasheet for the recommended curing time.
Can I apply solder mask multiple times on the same PCB?
It’s generally not recommended to apply solder mask multiple times on the same PCB as it can lead to uneven thickness and potential adhesion issues. However, in some specialized cases, multiple layers might be used for specific design requirements.
Conclusion
- Solder mask is a crucial element in PCB manufacturing, protecting the circuit board and preventing short circuits.
- Choosing the right type of solder and solder mask material is essential for the success of your PCB project.
- Applying solder mask requires precision and adherence to proper techniques, whether you make a PCB at home or use professional services.
- UV light plays a vital role in curing photoimageable solder masks, ensuring a durable and effective protective layer.
- Regular inspection and understanding of advanced solder mask techniques can significantly enhance the quality and performance of your PCB.
- As a leading PCB and PCB assembly manufacturer, we are committed to providing high-quality solutions and expertise to support your projects. Click here to learn more about multilayer PCB.
If you have any questions or need assistance with your PCB projects, please don’t hesitate to contact us. We are here to help you achieve the best results in your electronic endeavors.